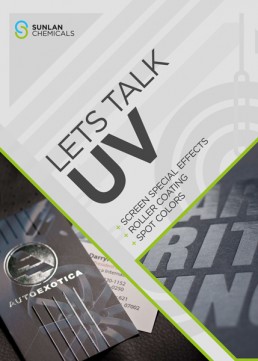
Fast Cure Speed, Satin Finish, Opaque
UV Screen Inks for Graphics & Packaging
Substrates
UV cure inks for flexible and rigid PVC, Polystyrene, HIPS, Polycarbonate, Acrylic, Cellulose acetate, pretreated polyethylene & polypropylene, fluted PP/corropack/sunpack and variety of papers.
Application
SUNLAN UV-2800 Series is the range of specially designed, fast curing, low odour UV screen printing inks with bright opaque shades. It has excellent flexibility, adhesion, weather resistance and most common solvent resistance. SUNLAN UV-2800 Series has high gloss and it thixotropic in nature giving excellent print sharpness. Widely applicable for outdoor display, advertising panels, signs, window graphics, labels and self -adhesive stickers and packaging containers. They are V -Pyrol free
Characteristics
- Excellent light fastness property due to specialized fade resistance pigments used (Blue wool scale 7 -8)
- Excellent flexibility, adhesion, weather resistance, alcohol and petrol resistance
- Very fast cure speed -suitable for rapid production
- Thixotropic in nature -does not drip through mesh when the machine is standstill
- Ideal for 4 -colour process inks job
- High colour strength for the range of shades and matching system
- Non-toxic, meets EN- 71 part 3 Toy safety standard for heavy metals
Curing
Ultraviolet cure inks are dependent on high dosage of UV light to initiate curing process that converts from wet to dry film. The light must see through or penetrate the layer of ink to achieve proper cure In a curing one 200-watt/inch (80 watt/cm) lamp, the cure speed 14-35 meter per minute are common. Cure speed depends on colours, film thickness, opacity and condition of the curing unit
Range
SUNLAN UV-2800 Series Matching System : Almost any shade can be matched by mixing the selective inks of the matching system
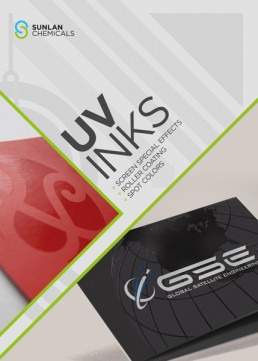
Process Colour
Magenta UV-2838 Density : 1:4
Yellow UV-2836 Density : 1:3 Black UV-2839 Density : 1:8 The density values are arrived at by using 150.31 T mesh. By adding Extender Base UV – 2850, the ink density can be reduced. The ink density can be increased by adding ink concentrated for the process colours in required proportion or by using a coarser mesh.
A coat of Over Print Varnish UV-2907 on the whole printed area will extend the period of out-door fade resistance and scratch resistance
Metallic Inks (Bronzes)
Rich Gold UV-2846
Rich Pale Gold UV-2847
Silver UV-2844
Metallic Clear Base UV-2845
The metallic ink made by mixing the metallic pigment with Metallic clear Base should be processed within 6-8 hours
Yield
Avery high yield of 75-95 sq. meters. with 140.34T to 165.31T can be achieved.
Auxiliaries
Reducer
Stir well before use. The viscosity of SUNLAN UV-2800 Series is supplied in a press ready condition for most printing applications. It may be necessary to thin slightly up to 3-5% with Curable Reducer UV-2856 cylinder press users as a special application.
Gel Tack Reducer UV-2857
Maximum 5% may be added to reduce tack and colour strength of ink without changing viscosity. UV-181 Screen Initiator for Black and Dark Colours Maximum 5% may be added to increase curing rate of UV inks. UV-450 Screen Initiator for White and Tint Colours. Maximum 5% may be added to increase curing rate of 2800 series inks.
Over Print Varnish UV-2835 : For improvement of fade resistance of the print
Accessories
Fabrics
SUNLAN UV-2800 Series prints and cures well through mesh between 355-420 per inch (140-165 per cm.) mono filament polyester Stencils : Stencil material must be solvent resistant and produce thin film stencil (3-6 microns over mesh.) Squeeze : Generally 70-80 durometer sharp edge squeezes are suitable.
Material Safety Data Sheet is available on request
Note : The Technical information sheet reflects the current state of our knowledge. This information is compiled based upon field experience and extensive laboratory testing. However, customers are requested to satisfy themselves that the products meet their requirements in all respects before.